


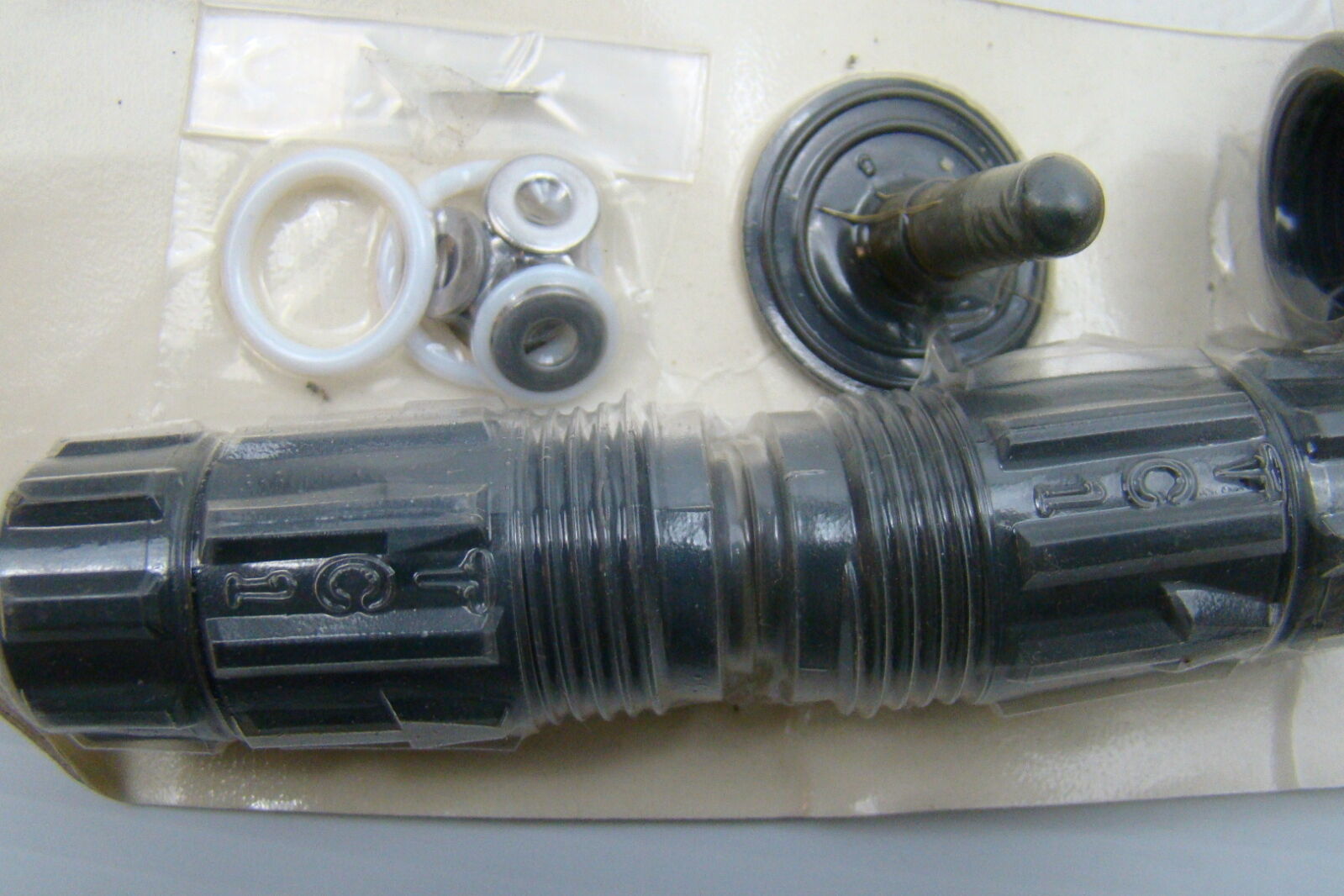
Neither of these considerations is so very critical for four-way valves. An excessive pressure drop will usually have a deleterious effect on the heat pump’s energy efficiency, while too small a drop can, for example, disrupt the otherwise stable behaviour of a servo-operated solenoid valve. Pressure drops are always important when it comes to dimensioning valve systems.
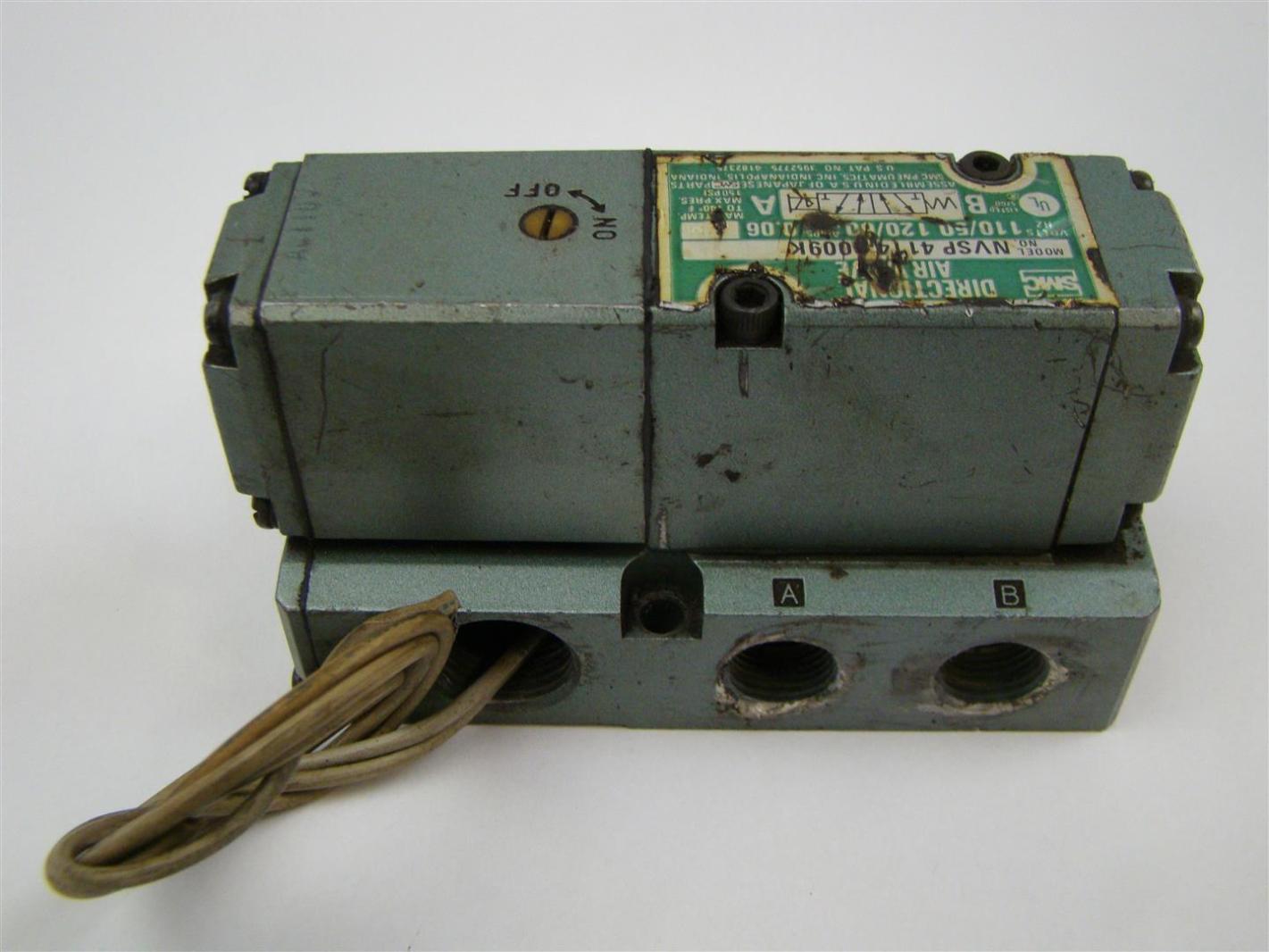
This allows the pressure on the right to be relieved via the central main connection at the bottom, causing the slider to move to the right. This is achieved by applying mains voltage to activate the coil of the solenoid pilot valve so that high pressure gas is introduced into the slider chamber from the left. In switch position 2 the hot gas makes its way from the top towards the left, while suction gas is simultaneously allowed to flow downwards from the right into the center. This displaces the slider towards the left and opens the main paths at the top, leading down to the right and from left to the center. At the same time the pressure at the left-hand side of the slider chamber can be relieved via the permanent suction connection, discharging the gas to the low pressure side. In this position, highly pressurized hot gas from the pilot line of the narrower connector enters the chamber containing the sliding mechanism from the right. In switch position 1 there is no voltage on the coil of the solenoid pilot valve. A standard four-way valve has only two switch positions – there are no intermediate positions. For the following description we shall suppose that the small (high pressure) connection is pointing upwards, the three other connections are pointing downwards, and the small solenoid pilot valve and its coil can be seen at the front of the unit.
